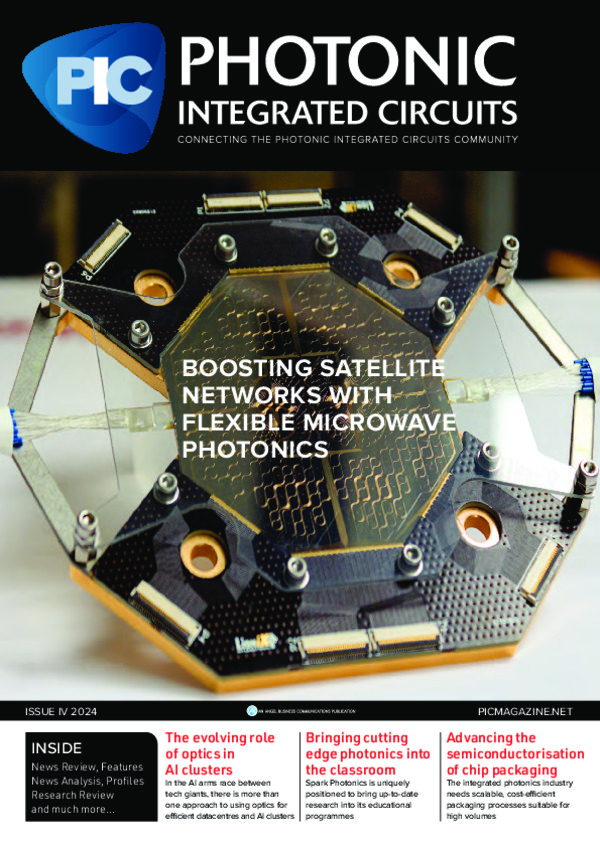
Advancing the semiconductorisation of photonic chip packaging
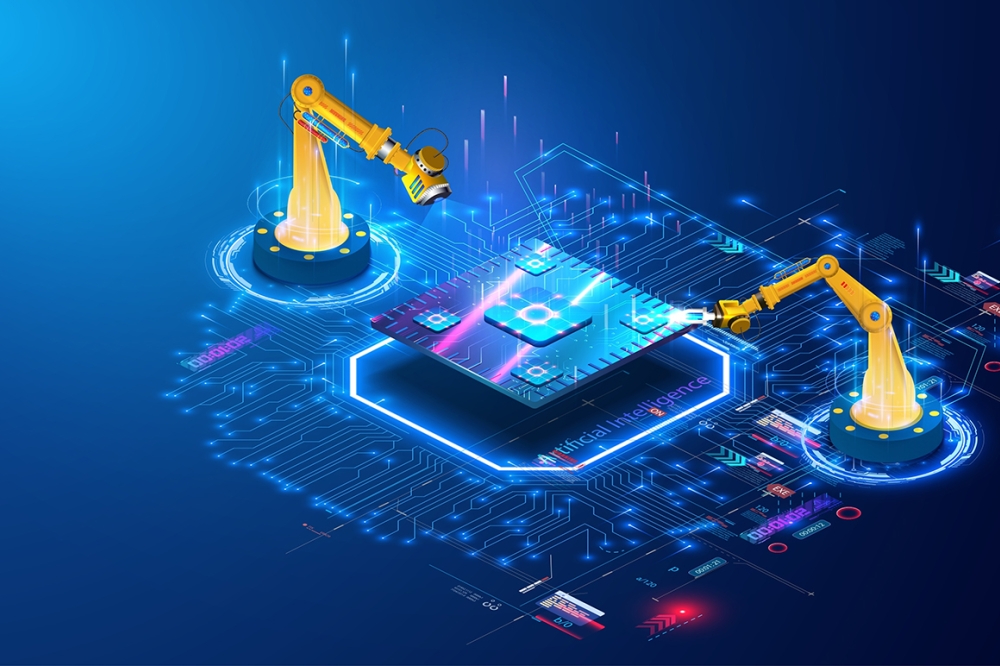
The PIC industry needs scalable, cost-efficient packaging processes suitable for high volumes, like those in traditional semiconductor manufacturing. The Chip Integration Technology Center (CITC) and vario-optics are working on multiple projects to this end, including co-packaging EICs and PICs on a glass substrate, and evanescent coupling into polymer waveguides.
By Nikolaus Flöry & Valentin Strässle, vario-optics, Sander Dorrestein, CITC, and Taynara de Oliveira, TNO Delft
Over the last decade, PICs and related technologies have matured tremendously and found use in a multitude of devices. Silicon photonics platforms, for example, have expanded their range of applications beyond transceivers to photonic computing, biomedical sensing, optical interconnects, and consumer applications.
The recent push towards adopting optical solutions in AI/ML hardware has further spurred the development of multi-chip modules that require high-density electrical and optical interconnects.
These upcoming generations of PIC designs present common challenges in electrical and optical assembly and packaging, namely: increasing density (more functions per unit area); increasing bandwidth and reaching higher data rates while maintaining signal integrity; and developing cost-effective assembly processes for high-volume manufacturing.
Figure 1. Traditional way to optically couple to a PIC using
direct attach fibre arrays units (FAUs). Such assemblies are suitable for
companies seeking to assemble and package their (first) integrated photonic
dies for prototyping. However, due to many discrete components involved,
cumbersome footprints and loose fibres within the setup, such solutions are not
suitable for mass-scale fabrication flows.
So far, state-of-the-art assembly technologies developed for foundry-produced PICs have focused primarily on supporting businesses with prototyping, low-volume manufacturing, and fibre pig-tailing (Figure 1). This has resulted in a poor level of standardisation and highly complex systems and processes that are only suitable for low volumes, making it challenging for new companies to adopt these methods and establish a viable business model in the market.
Another factor contributing to this landscape is that PIC products need to be considerably differentiated, both to achieve their technological aims and to stand out commercially. However, this leads to high assembly costs, especially compared to those in the established semiconductor industry; assembly makes up about 80 percent of the total costs of an integrated photonic device, compared with just 20 percent for typical semiconductor devices. To provide cost-effective photonics products – and thus keep up with increasing demands in the future – assembly methods must be simplified and made scalable. Addressing these cost challenges is essential for PICs to transition from niche solutions to mainstream applications, especially in consumer electronics, telecommunications, and biomedical devices, where affordability and scalability are critical.
Figure 2. Concept for advanced packaging for integrated
photonics. On the top side of a glass substrate there is an optical
redistribution layer, and on the bottom side an electrical one. Combined they
enable chip-to-chip and chip-to-world communication.
Fortunately, the semiconductor industry offers a range of assembly and packaging processes with proven scalability and cost efficiency, presenting valuable insights and methods that can be adapted for PIC packaging. However, integrated photonics has unique requirements, so these processes must be tailored to meet the specific needs of high-density optical interconnects. This adaptation process, termed the “semiconductorisation” of PIC packaging, focuses on simplifying assembly steps while enhancing accuracy and scalability.
For instance, streamlined assembly techniques, like automated passive alignment, can significantly reduce per-unit costs. Recent pilot projects show that simplified panel-level packaging can achieve cost reductions of up to 30-40 percent compared to traditional fibre pig-tailing and discrete component assembly. Such benchmarks offer a promising roadmap for further cost-cutting strategies as PIC technology scales to higher production volumes, potentially making photonic solutions more accessible for a range of applications.
Figure 3. Optical module with pluggable fibre interconnect.
Scalable co-packaging of chiplets
Supported by the Dutch Growth Fund PhotonDelta, the Chip Integration Technology Center (CITC) is developing a scalable panel-level assembly concept addressing many challenges of integrated photonics packaging. CITC is collaborating on this project with vario-optics, which provides the key optical interconnect technology. The concept utilises advanced assembly technologies from the semiconductor industry, but is tailored to co-package EICs and PICs in a single package. In other words, this programme adds the “optical element” of advanced assembly at the panel level.
This concept, shown in Figure 2, is based on a panel-level fan-out design, where electrical and optical chiplets are mounted on the panel. Electrical and optical redistribution layers (eRDLs and oRDLs) enable chip-to-chip and chip-to-world communications in both domains. An oRDL is produced on one side of the panel and an eRDL on the opposite side. Using through glass vias (TGVs) the electrical interconnects cross from one side of the panel to the other. A flip-chip bonding process mounts both EICs and PICs on the panel.
Once the panel is populated, the assembly is covered by an overmoulding compound to protect sensitive components. Single modules are then created by cutting the panel in a conventional wafer dicing process. After this step, the module’s optical interface is accessible through a mechanical interface, which an optical connector can be plugged into, as shown in Figure 3. The end user can assemble the module according to the needs of their particular application, either in a land grid array or ball grid array.
Bearing in mind the key targets of scalability and cost-efficiency, every choice related to this packaging platform is made with the aim of simplifying the assembly process. This means using known semiconductor assembly processes, realising relaxed alignment tolerances at the panel scale or wafer scale, and enabling short process times.
Figure 4. Planar polymer waveguide platform. Typical mode
field diameters are: 1 µm for InP; 2 µm for silicon nitride; about 10 µm for
SMF28 glass fibre; and adjustable between 4-8 µm for polymer waveguides.
Photonic interposer based on PCBs
Many of the features and benefits of optical interposers stem from the semiconductor and microelectronics industry. The key difference in applying this concept to photonics is the addition of an oRDL that is compatible with various substrates (PCB, glass, silicon) and can be connected to photonic chips. Planar waveguides based on polymer or glass are an excellent candidate to fulfil these requirements.
One of the biggest challenges in coupling light into PICs is their inherently small mode field diameter (MFD). PIC platforms with very high confinement, such as InP, can exhibit MFDs of the order of only 1 μm. Coupling standard SMF-28 glass fibres to such small MFDs results in high optical losses due to the mode field mismatch. Although spot-size converters are available on most PIC platforms today, they typically require additional steps in the manufacturing process and exhibit large footprints, both of which increase the costs per unit area on the wafer. Moreover, to connect them to glass fibres or fibre arrays, additional fan-outs are necessary.
Depending on the pitch size (127 μm or 250 μm) and number of I/Os, spot-size converters and fan-outs consume a comparatively large area of the wafer.
For economic reasons it therefore makes sense to relocate these features to another platform, and polymer waveguides can perform this task. They can be manufactured in large quantities on different substrates such as glass or silicon wafers or PCB panels using UV lithography. Polymer waveguides also require far fewer process steps, decreasing the costs per area. Larger features like spot-size converters, fan-outs, splitters, and combiners can therefore be fabricated at minimal cost.
Furthermore, the dimensions of the cores and thus the MFDs of the polymer waveguides can be varied without any additional effort, even on the same chip (see Figure 4). Thus, different PIC technologies like silicon photonics, silicon nitride, and InP as well as glass fibres can easily be connected. All these capabilities make polymer waveguides a first-class technology platform for hybrid integration and photonics at the PCB and interposer level.
Standard PCBs can include features such as high-speed RF interfaces, (glass) interposers, thermal dissipation layers, and electrical vias. Depending on the application, the polymer waveguides can be fabricated on top of the PCBs or sandwiched into them to form the optical connections of the electro-optical board. The PCB can also be substituted with other carriers such as silicon wafers or glass sheets. As polymer waveguide technology has advanced, it now supports single-mode operation at most common wavelengths (O-, C-, 850-nm-band). Moreover, polymer waveguides show high power damage thresholds, good environmental stability, and compatibility with reflow soldering processes.
Figure 5. Comparison of different coupling schemes.
Low-loss coupling: the holy grail
There are several ways of optically connecting PICs to oRDLs: edge coupling, surface grating coupling, and surface coupling by adiabatic or evanescent field couplers. The most important factors in choosing a coupling technique are: alignment accuracy requirements, optical losses, wavelength variation sensitivity, polarisation sensitivity, and testing possibilities. Figure 5 compares the advantages and disadvantages of different optical coupling schemes.
Edge coupling is a well-established scheme suitable for a variety of PIC technologies. Many concepts have been developed to overcome tricky alignment routines. In the H2020 project QAMeleon, for example, vario-optics developed a micro-machined silicon carrier to act as a substrate for both an active InP chip as well as a passive polymer fan-out circuit (see separate box). The 3D patterned carrier enables highly accurate passive alignment of the optical parts.
At the same time, recent improvements in assembly equipment and alignment routines have made active alignment more compatible even with high-volume manufacturing. CITC is investigating test vehicles in which a fibre assembly unit (FAU) with standard SMF-28 fibres is bonded to a polymer waveguide chip (Figure 6). The technique involves actively aligning the outermost fibres of the FAU to optical loops on the polymer chip. The two parts are bonded together when the signal of both loops is optimised. In a second step, the package is positioned and bonded to a silicon nitride PIC with similar alignment loops and small MFDs of 2 μm.
Figure 6. A concept for simultaneously interfacing a polymer
interposer with both an FAU and a small-mode-field PIC silicon nitride PIC,
involving active alignment.
This configuration has demonstrated coupling losses on the order of only 1 dB per facet (polymer-to-PIC) – significantly better than direct fibre-to-PIC connections, which typically have coupling losses of close to 3 dB. Polymer waveguide interposers therefore meet the requirements for low-loss fibre-to-chip coupling or even chip-to-chip coupling.
However, there are limits to how much this technique can reduce the overall system losses, even with tailored polymer waveguide geometries. This is because there are geometrical limitations in optimising for two different interfaces within one waveguide, as well as limits to alignment accuracy. Using an alternative approach of evanescent field coupling offers a viable solution for circumventing these constraints.
Evanescent surface coupling
Evanescent coupling, commonly also referred to as adiabatic coupling, involves an energy transfer between overlapping evanescent fields in two waveguides. This technique relies on a near-field interaction at the surface interface, so it is essential to minimise the gap between the waveguide cores to increase the energy efficiency of the transfer. Both cores must therefore be exposed to allow for a low-loss coupling.
Figure 7 presents a schematic representation of the evanescent field coupling mechanism. In this process, light is out-coupled from the silicon nitride PIC via an inverted taper, which narrows to an optical tip, forcing the mode field out of the waveguide. During the assembly phase, this tapered section is aligned in proximity to the polymer waveguide on the oRDL, enabling efficient mode transfer whereby the light is captured and guided towards the package interface.
Results of design simulations highlight how optimising both the silicon and polymer waveguide structures can yield exceptionally low loss. For instance, using a 420 µm taper length with high refractive index contrast polymers results in coupling losses as low as 0.2 dB at a wavelength of 1550 nm. Extending the taper length to 900 µm further reduces the coupling loss to just 0.08 dB, which is very promising compared to the state of the art.
Furthermore, redesigning not only the taper but also the overall chip – including adjustments to refractive index contrast, cladding materials, and other factors – can minimise the footprint of these interconnects to hundreds of microns while maintaining coupling efficiency above 95 percent.
This approach also relaxes lateral alignment tolerances to
approximately ±2 µm for both transverse electric (TE) and transverse magnetic
(TM) polarisations. Previous experimental studies, conducted independently by
IBM and vario-optics, have already demonstrated the strong potential of this
technique, achieving total coupling losses of less than 1.2 dB for a
fibre-to-polymer-to-PIC setup, and showcasing the PCB-integration of adiabatic
coupling interfaces, as demonstrated within the
EU project ICT-STREAMS (see separate box).
While these results prove the viability of this scheme, previous realisations have been constrained by non-ideal planarity of PCB substrates and the limited availability of PICs with accessible core layers.In recent years, however, several foundries have added these features to their PDKs. Beyond that, the use of a glass substrate for both eRDLs and oRDLs is a great choice in terms of planarity for such an interface, finally allowing full exploitation of the advantages of evanescent coupling.
Figure 7. Results from optical simulations of an adiabatic
coupling interface. The modelling allows the extraction of critical taper
dimensions on silicon nitride. Coupling losses of ~0.08 dB (98 percent coupling
efficiency) can be achieved for a taper length of 1000 µm at a wavelength of
1550 nm. This is much more efficient compared to the industry standard of 1 dB
for regular edge-coupling interfaces.
Outlook on scalable manufacturing for PIC packaging
Advanced and scalable panel-level processes, together with
efficient coupling methods, hold great promise to fulfil the key requirements of future PIC packaging: low-loss optical interconnections with << 1 dB (20
percent) optical loss from PIC to oRDL; relaxed alignment tolerances >> 1 µm; and
cost-effective assembly methods of PIC to substrates with automated passive
alignment.
Both edge coupling and evanescent coupling schemes used in such a photonic interposer platform can provide excellent performance.
Each use-case requires a system-level evaluation to identify the most suitable coupling scheme, balancing efficiency, assembly tolerances, and most importantly cost per assembly.
In all cases, integrating both electronics and photonics in a single package is a key prerequisite for the successful semiconductorisation of PIC assembly and photonic packaging.