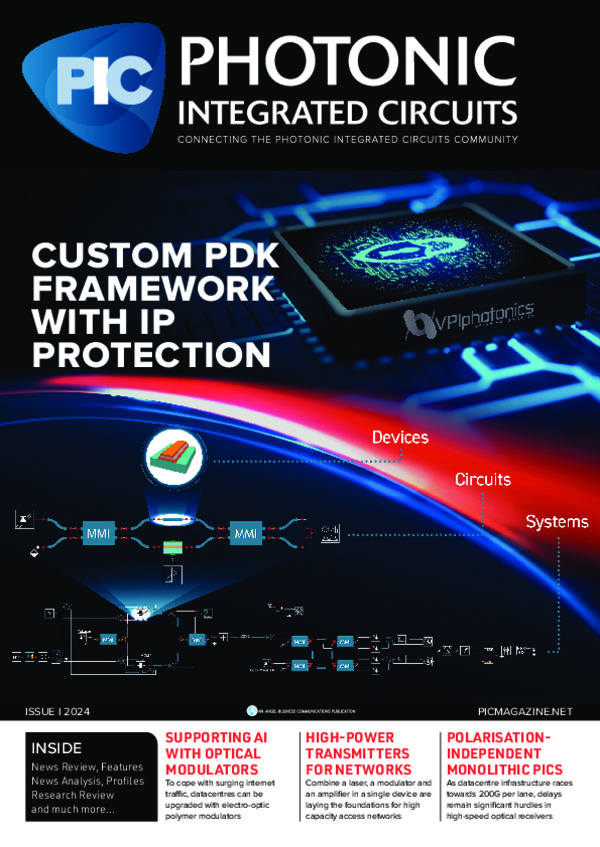
The best of both worlds: Design freedom and IP protection
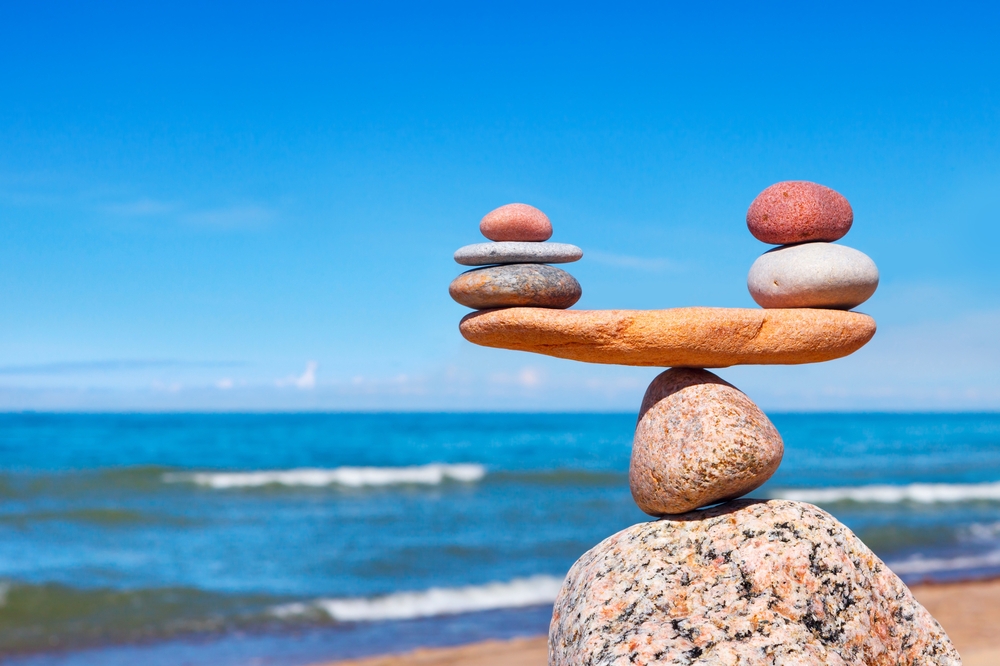
VPIphotonics empowers foundries and fabless companies by giving them the freedom to customise PIC designs using process design kits while also ensuring the security of intellectual property.
BY ANDRZEJ POLATYNSKI, STANISLAU SAVITSKI, CHRIS MALONEY, AND ANDRÉ RICHTER FROM VPIPHOTONICS
In recent years, rapid advancement in the PIC industry has led to the emergence of many advanced technological platforms for photonic chips. Those platforms are commercially available to enterprises and scientific institutions, often after passing long development cycles. Modern photonic design automation (PDA) tools provide access to these technologies via professional software environments, which support the design of application-specific photonic circuits and systems with foundry-dedicated building block libraries, better known as process design kits (PDKs). For instance, this industry ecosystem allows end users to create PICs whose spectral range of operation extends beyond the C-band, enhancing their use in telecommunications and data transmission networks, sensor systems, and biomedical devices.
Figure 1. Customisation of the PDK building blocks (BBs) based on the
example of an imbalanced 2x2 multi-mode interferometer (MMI).
However, since there is a need to balance customisability with intellectual property (IP) security, end users rarely have complete freedom in how they use PDKs. Photonic foundries that open their technology to third-party users specify stringent constraints describing their fabrication processes and design rules. Typically, only limited building block geometry and performance data is shared, as these details represent critical IP belonging to a foundry, collected after many years of development. Foundries limit the information accessible to end users to safeguard their proprietary knowledge, meaning that end users can often use only a basic subset of the platform’s capabilities. They are usually also restricted to utilising predefined and optimised building blocks, providing only a few parametrised attributes to design their PIC.
Figure 2. Generation of a custom PDK in VPIcomponent Maker Photonic Circuits.
To enable the broadest range of applications, and fulfil the PIC industry’s needs, PIC designers will need access to more flexible PDKs, but there are two main challenges to overcome. First, there needs to be a way to customise existing building blocks without breaching the foundry’s IP. Second, end users need to be able to create new custom building blocks, either based on device-level simulations or experimental data. Solving these issues would allow the designer to supplement existing PDK libraries with new building blocks, opening a wide range of new applications.
This is where VPIphotonics comes in. The company’s solution is to provide a framework for generating custom PDKs, allowing designers to enrich existing commercial PDKs and to create
new PDKs for other PIC platforms. This framework offers its users complete freedom to customise an existing PDK, allowing them to add complementary building blocks and enabling fabless companies to develop their own internal PDKs while protecting their IP.
Custom PDK generation
The process of generating a custom PDK is depicted in Figure 2, where the starting point is a demonstration library, here called PDK DemoFab. The user can specify a custom PDK name to create a new library, which includes all the necessary features of a standard PDK, including design automation macros, custom user interface toolbars, building block templates, and their links to layout descriptions. This process can be further customised to adapt the template models to the designer’s unique requirements.
Figure 3. Block description of the layout-aware schematic-driven design methodology and its implementation with VPIcomponentMaker Photonic Circuits [2]
Moreover, users can add modules from commercially available PDKs. All added foundry components are directly encrypted to protect the foundry IP, and the user can automatically encrypt their custom building blocks to protect their own IP when shared as part of a custom PDK. Usage of the foundry components typically requires a confidentiality agreement with the fab and the allocation of a software license dedicated to the foundry PDK. Customised building blocks are licensed under the custom PDK framework and can be encrypted directly by the user. Thus, sharing those components does not require additional licenses and can be done directly by the user who developed the custom PDK.
An essential feature of professional circuit design tools is the capability of simulating fabrication tolerances. Therefore, just as with standard foundry PDKs, tolerances can be included in custom PDK libraries by adding the performance distribution directly to the description of a building block. The design process and challenges are identical in custom and commercial foundry PDKs and are described in detail in previous literature [1].
Design workflow, implementation, and interfaces
The workflow for using a custom PDK is equivalent to that of a standard PDK, utilising a layout-aware schematic-driven design methodology, as shown in Figure 3. The designer can use custom building blocks and standard PDK components to create a circuit design that can be simulated and further optimised. The user can also perform a tolerance analysis of their design. Thanks to the layout-aware simulation approach, the layout of the designed chip can be directly verified and visualised from the schematic perspective at any time. Moreover, the designer can utilise “elastic” components [2], ensuring that the waveguides used to connect building blocks will be automatically routed to fulfil the design requirements.
Figure 4. Demonstration of the automated export from the simulation schematic to various layout tools.
A typical simulation PDK must include building blocks verified by the foundry with proper interfacing between the simulation model and the device layout. The requirements are the same for a custom PDK, but now the PDK designer is responsible for the functional building block instead of the foundry. To ensure that the custom module performs correctly, designers must rely on their knowledge from previous foundry runs or device-level simulations. Characteristics from these sources can be included in the PDK library, allowing for circuit and system-level designs. The interface between the layout and simulation tool means that, with the press of a single button, the layout can be automatically exported from the simulation schematic. The designer can define a custom layout description compatible with a foundry’s layer definition. Within the custom PDK framework available in VPIcomponentMaker Photonic Circuits, the interface includes templates for PDK module generation with example layout descriptions in several layout tools, as shown in Figure 4. Furthermore, dedicated macros can help the designer build custom PDK building blocks automatically by loading data files in a standardised format or via the interface with a device-level simulation solution called VPIdeviceDesigner.
Figure 5. Demonstration of custom PDKs dedicated to various platforms developed under European and regional R&D projects, including polymer, silicon nitride (PolyChrome project, polychrome-berlin.de), lithium niobate (ELENA project, www.project-elena.eu), and germanium on silicon (MIRPIC project, www.mirpic.eu). Various waveguide colours determine different modules’ cross-sections.
Many platforms, one solution
Another advantage of the custom PDK is that it is inherently platform agnostic; users can easily adapt it to any material, operational wavelength, and manufacturing process. Within the current state of the art, custom PDKs have been demonstrated for various platforms, including indium phosphide, lithium niobate, polymer, silicon, silicon nitride, and germanium on silicon. Several examples are shown in Figure 5. Achieving both flexibility for PIC designers and IP security presents an inherent challenge for the end users of PDKs, but VPIphotonics’ custom PDK framework provides a flexible solution for foundries and fabless companies alike. Enabling the customisation of foundry building blocks and the development of customised PDK libraries, this solution offers all the features of a typical foundry PDK, including IP protection, while being easy to share and giving designers the freedom to add and adapt building blocks to their specific needs.