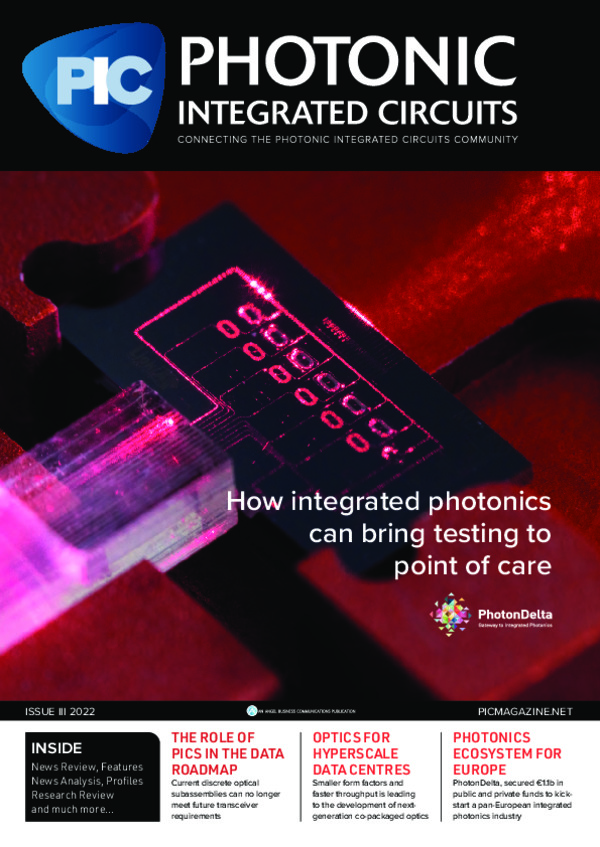
PIC T&M must evolve to meet passive and active component needs

Datacentre developers look to PIC-based transceivers as a means to handle increasingly large volumes through greater efficiency, smaller size and cooler operating temperatures. But datacentres typically utilize 50,000 or more transceivers, which creates a testing conundrum and bottlenecks for manufacturers. The experts at EXFO describe how T&M is evolving to meet these demands.
By Aldo Gutierrez, Ph.D., EXFO Product Line Manager, EXFO
Network transformations are underway around the world at a breakneck rate, as operators strive to extend the benefits of high-speed optical networking and 5G mobility to their customers. Enabling those transformations are the research, design, and manufacturing innovations being implemented by component manufacturers working to keep pace with the evolution of speeds and feeds at the network and data center level.
Each data center can have as many as 50,000 transceivers deployed, and transceiver manufacturers are challenged to produce thousands of devices daily. There is growing demand for connected devices and integrated optics at the component level that are faster, highly reliable, and more compact than ever before.
One of the biggest challenges is to produce high-quality, advanced transceivers in volume while ensuring that heat production can be managed for these devices. Photonic Integrated Circuit (PIC) solutions are being adopted by transceiver manufacturers to address the reduced size and complexity challenges while also addressing heat management issues experienced in today’s data centers.
This article will examine the trend to adopt PIC-based transceivers, and how testing both passive and active components is key to enabling production of next-generation, PIC-based transceivers.
Today’s reality
By using PIC technology to consolidate and integrate various components on a single chip, functionality can be increased while increasing density, lowering the cost of production, and reducing energy requirements. PIC testing can support the new generation of transceivers including 5G wireless transceivers, 800G transceivers, and coherent modules for high-speed networking. While in the past transceivers were only electronics-based, the new wave of transceivers incorporates both optical and electrical elements, increasing the complexity of design and production.
Testing active components with OSA and optical oscilloscope
Testing – the critical element
Even with design improvements enabled by PIC solutions, there are still challenges inherent in delivering thousands of components each day. There are often bottlenecks on foundry lines due to the sheer volume of units and even the multiple ports-per-unit needing testing. Component testing throughout the design, foundry, and packaging stage is critical.
That means testing must be a consideration from the design stage through ports-per-unit to ensure that the test process is simplified, test time per unit is reduced, and bottlenecks are avoided. And fortunately, innovation in light coupling methods has made wafer-level testing possible for mass production. EXFO is uniquely positioned as the only test & measurement (T&M) solutions provider that can offer both passive and active component testing.
Testing active components with OSA and optical oscilloscope
Testing active optical components
Testing active components such as modulators, lasers, and amplifiers found on PICs is usually done using general test instruments. An optical spectrum analyzer (OSA) can be used to measure the spectral signal, and an optical oscilloscope
is used to measure the eye diagram of light sources.
The latest OSAs are extremely fast and can perform up to five scans per second at speeds of 2000 nm/s, enabling real-time component alignment with sufficiently high resolution to allow measurement of key parameters such as optical signal-to-noise ratio (OSNR) and side mode suppression ratio (SMSR).
Swept IL measurement of ring resonator performed using the CTP10 test platform
Testing passive components
Testing PIC-based passive components is often challenging due to the high port count of some components like arrayed waveguide grating (AWG) or the sheer number of components to test on a single die. A component test platform is a multiport detection system that operates in conjunction with a continuously tunable laser to measure optical insertion loss, return loss and polarization-dependent loss across the laser’s spectral range. The method yields optical spectrum quickly and with a high wavelength resolution, typically on the order of a picometer.
EXFO’s CTP10 passive optical component tester with T100S-HP high-dynamic range tunable laser enables swept laser testing of passive optical components at a picometer resolution and at high speeds, even under the most stringent conditions. The auto-alignment capability of the CTP10 allows for finding the optimum optical in- and output connections of the PIC on wafer in the fastest time possible.
The CTP10 operates from 1240 to 1680 nm and covers a wide range of applications, including telecom, sensing, and LiDAR. Its electronics and internal processor simplify data transfer. It can be remotely controlled using SCPI commands, facilitating integration as part of a larger-scale automated PIC test setup, which helps keep testing time to a bare minimum.
Automated component testing
With more functionalities being integrated onto a single PIC, new functional tests like bit-error-rate (BER) or eye diagram are needed in addition to the conventional parametric tests. This is true even at the wafer and die levels in order to fully characterize these increasingly more complex PIC devices.
Test & measurement companies, including EXFO, are leveraging automation to enable full control of end-to-end testing from wafer and die to packaging, as well as to simplify configuration and test processes – and to reduce time required between various test stages. That’s a challenge because each application demands a unique PIC solution that’s readily customized and quickly reconfigurable to optimize testing. Manufacturers need a turn-key solution that enables end-to-end testing in volume production settings.
EXFO continues to invest in automation and has made advances with flexible PIC test solutions that can scale to meet future requirements. EXFO has collaborated with other industry innovators to deliver customized solutions. To best respond to varied customers with diverse product lineups, latest technology in ultra-high precision alignment systems, collision avoidance sensors, temperature control, machine vision, and electronic testing and photonics often need to be combined to provide a simple-to-use interface.
The future for PIC solutions
PIC technology has also increased in importance for industry segments beyond optical communications including co-packaged optics for next-generation high-speed transmission, automotive LiDAR for autonomous vehicles, and quantum communications for AI or machine learning applications.
These new PIC applications use diversified technology platforms and PIC designs, and also bring new challenges to PIC fabrication and testing. More modular and scalable PIC production and testing solutions will be needed to support wide-ranging PIC designs and to create the economy of scale needed to ensure competitive cost structure and return on investment. And testing from design to packaging to deployment will be key to success in providing next-generation PIC-driven solutions.
For more information on PIC testing solutions from EXFO, download the company’s application note: https://www.exfo.com/en/testing-next-gen-pic-based-transceivers