Researchers Share Recipe for "˜DIY' Hyperspectral Imagers
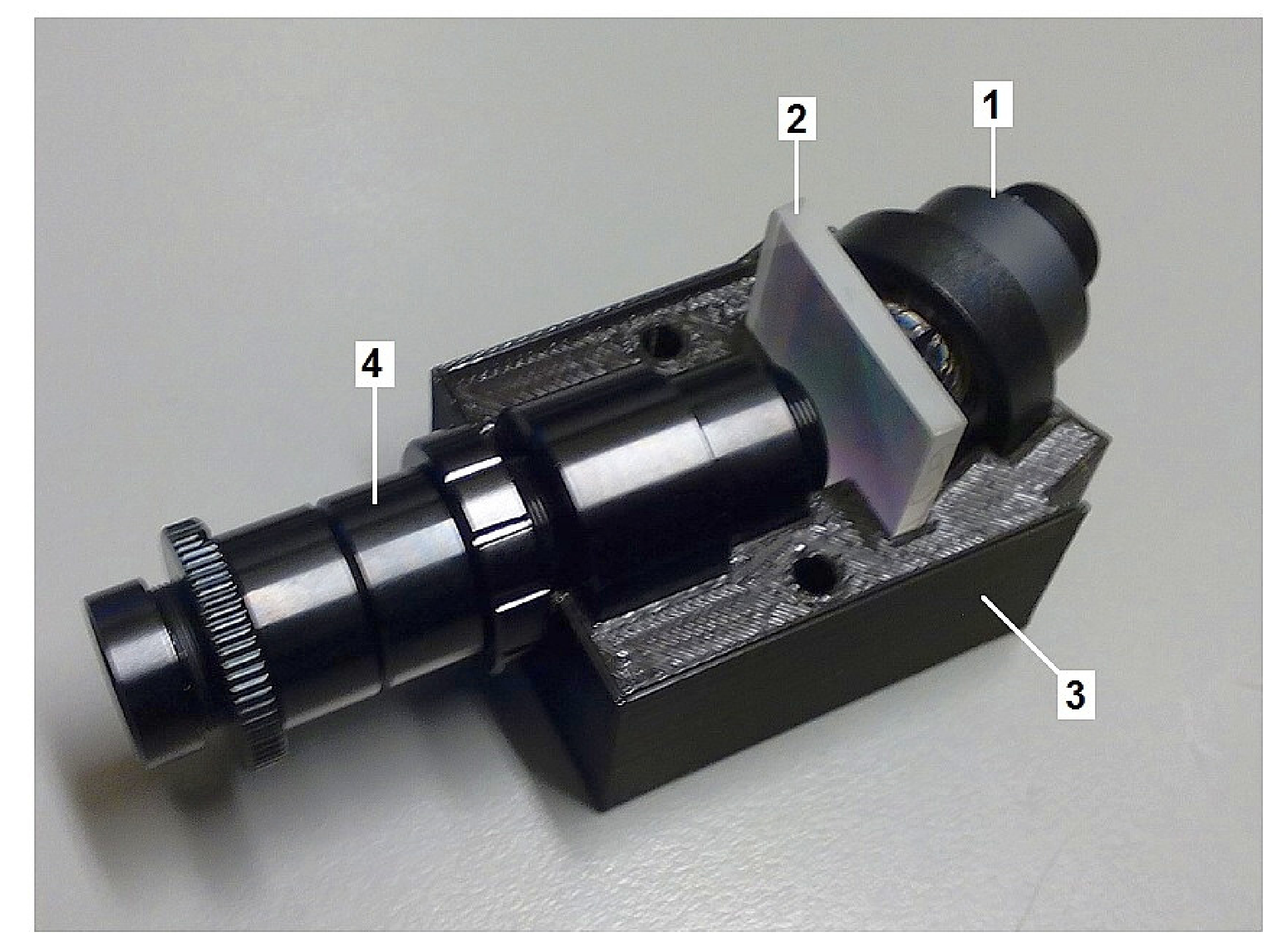
Researchers used 3D printing to make an inexpensive and small hyperspectral imager. Feasibility tests showed that 3D printing can be used to produce prototype parts sufficiently accurate for optical systems. Shown is the transmission grating holder: (1) detector lens, (2) 25 à— 25 mm2 600 grooves/mm transmission grating, (3) 3D printed grating holder, and (4) Collimator-slit-front-optics assembly.Courtesy of Fred Sigernes, University Centre, Svalbard.
Norwegian researchers from the University Centre in Svalbard have used 3D printing and low-cost parts to create an inexpensive hyperspectral imager that is light enough to use on drones. The visible-wavelength hyperspectral imager (HSI) weighs less than half a pound, according to researchers, and can be built for as little as (USD) $700. Traditional hyperspectral imagers can cost tens of thousands of dollars and are both too bulky and heavy for drone-based aerial applications.
The research team has provided directions for creating the imagers; the paper is available through the Optical Society of America's Optics Express newsletter. The new imagers employ the so-called "˜push-broom' technique, an approach that uses precise line-scanning to build a spectral image. The researchers added a stabilization system to their setup so that a drone's movement would not distort the image as it was being generated.
"Push-broom hyperspectral imagers typically require expensive orientation stabilization," said researcher Fred Sigernes. "However, you can now buy very inexpensive gyroscope-based, electronically stabilizing systems. The advent of these new systems made it possible for us to make inexpensive hyperspectral imagers."
The dispersive element housings were printed using a thermoplastic 3D printer combined with S-mount optical components and commercial off-the-shelf camera heads. The 3D printer eased the process of making the custom optics holders needed for the imagers.
"Making items in metal is time-consuming and can be very expensive," said Sigernes. "However, 3D printing with plastic is inexpensive and very effective for making even complex parts, such as the piece needed to hold the grating that disperses the light. I was able to print several versions and try them out."
Four models were constructed, each with a mass less than 200 g and a spectral range in the VIS to NIR part of the electromagnetic spectrum. The bandpass ranged from 1.4 to 5 nm.
Researchers tested one of their prototypes aboard an octocopter drone equipped with a two-axis electronic stabilizing system. The hyperspectral imager performed well and was able to detect landscape features, such as vegetation and bodies of water. Three test experiments with motorized gimbals to stabilize attitude showed that the instruments were capable of push-broom spectral imaging from various platforms, including airborne drone to handheld operations and three-axis electronic stabilizing systems. For one experiment, researchers swept the imager across a computer screen displaying a fruit collection, acquiring 571 spectrograms in 22 s.
These feasibility tests showed that 3D printing could provide the level of accuracy needed to produce prototype parts for optical systems. The printed plastic parts were lightweight and strong enough to keep the overall system light and small. Researchers suggest that after testing, metal versions of 3D printed parts could be ordered if desired to create imagers that would be more durable.
Although the new DIY imagers don't provide the sensitivity of traditional hyperspectral imagers, their performance is sufficient for mapping terrain or detecting ocean color in daylight. The researchers are now working to improve their imager's sensitivity by making slightly larger versions of the instruments that would still be small and light enough for use on drones. Improving the sensitivity of the imagers would result in higher-quality data.
"There are many ways to use data acquired by hyperspectral imagers," said Sigernes. "By lowering the cost of these instruments, we hope that more people will be able to use this analytical technique and develop it further."