Photonics alignment systems offer six degrees of freedom
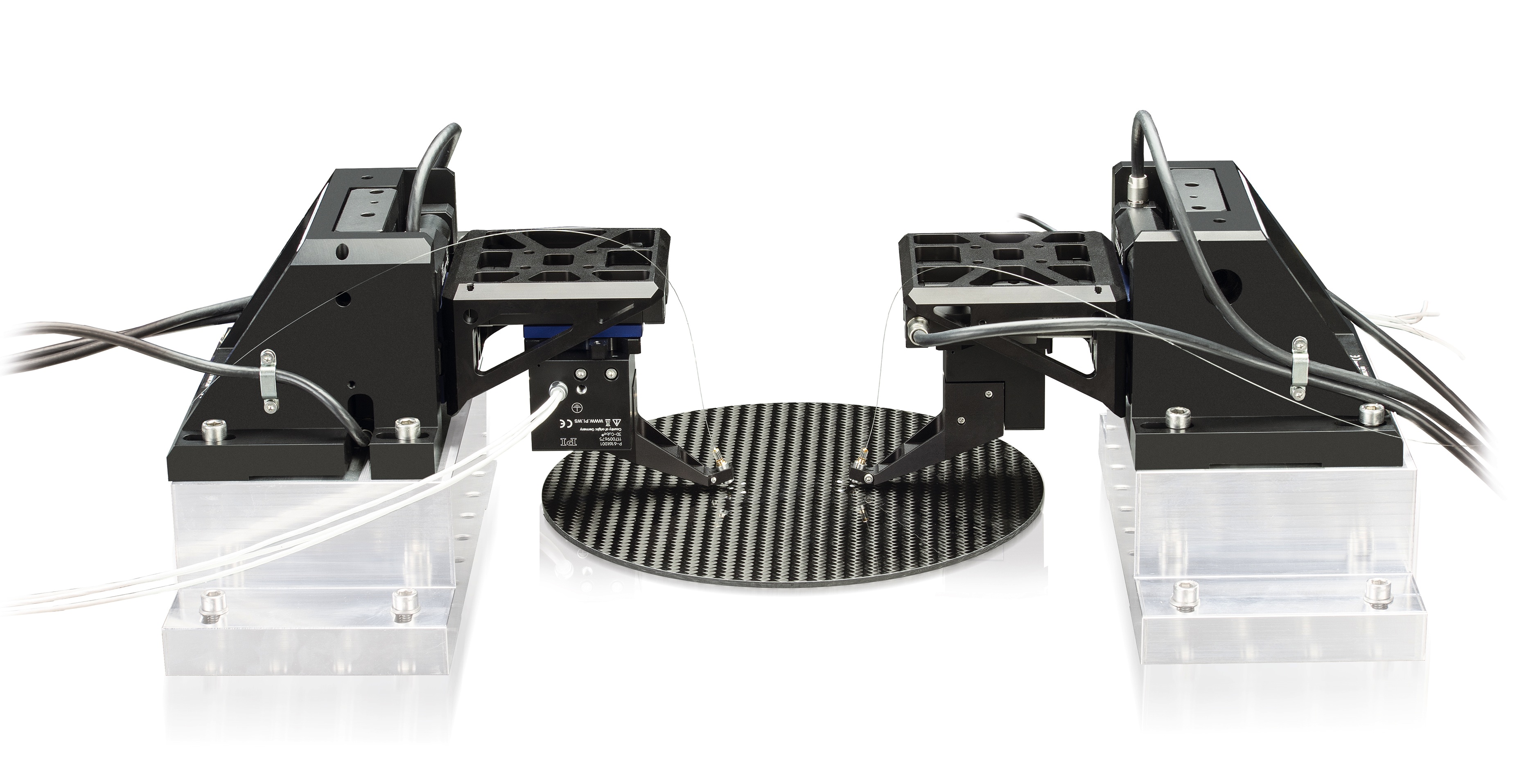
Physik Instruments's two high-precision photonics alignment systems enable several fibres to be aligned in seconds
During production and inspection of components with optical data transmission, it is important to align fibres or fibre arrays for optimum connection with the highest possible accuracy. Position tolerances way under 50nm are usual and multi-channel inputs and outputs require simultaneous alignment in several axes.
PI (Physik Instrumente) has added two high-precision photonics alignment systems to its range that enable several fibres to be aligned in seconds. Both systems are based on a design that consists either of three stacked linear axes (F-712.MA), or "“ if rotary motion is required "“ a parallel-kinematic hexapod (F-712.HA) combined respectively with a nanopositioner.
The parallel kinematics and the stacked axes with their motorised drives enable longer travel ranges of a few millimeters for coarse positioning, and at the same time, the NanoCube positioner ensures fast scanning motion and dynamic compensation of drift effects.
According to the company, flexure guides and all-ceramic insulated piezo actuators guarantee a long lifetime. Position sensors on all drives prevent collisions, for example, with an expensive silicon wafer.
Both systems are available for either single-sided or double-sided positioning tasks. The scope of delivery includes a high-performance digital controller (E-712), firmware routines with algorithms for very fast positioning, and an extensive software package. The matching hexapod controller (C-887) is also supplied with the parallel-kinematic set-up.
The stacked system for positioning fibres or optical components operates in all three axes for coarse positioning with travel ranges from up to 25 mm at a minimum incremental motion of 2 µm, and a maximum velocity of 20 mm/s.
For hexapods, the travel ranges in the X, Y, and Z direction are ±6.5; ±16 and ±8.5 mm, and for the three rotational axes at ±14.5, ±10, and ±10 degrees. The minimum incremental motion is 0.1µm respectively.
The system operates at a maximum velocity of 10 mm/s and PI says it can delicately position the user-defined centre of rotation (pivot point) at any point in space, even at different angles, for example, when positioning fibre arrays.
The NanoCube, which takes care of the fine positioning for both systems, operates with travel ranges of 100 µm in all three axes and a minimum incremental motion of 2.5 nm. The positioning time for area scanning over 100 µm x 100 µm is under 1 second at a maximum deviation of the peak intensity of 0.02 dB.